CASE STUDY
Development of 2 ATEX/IECEx Certified Hydraulic Power Units for Tilting Chute on Ship Loader
APPLICATION GOAL
Sector and Function
The hydraulic power units were developed for the movement of the tilting chute arm mounted on a shiploader system, designed for loading bulk materials from shore to ship. The application operates in environments classified as potentially explosive.
Customer Requirements
The client required the entire mechanical assembly (power unit + cylinders) to be ATEX/IECEx certified by a third-party body (TÜV), thereby ensuring regulatory compliance for use even outside the EU.
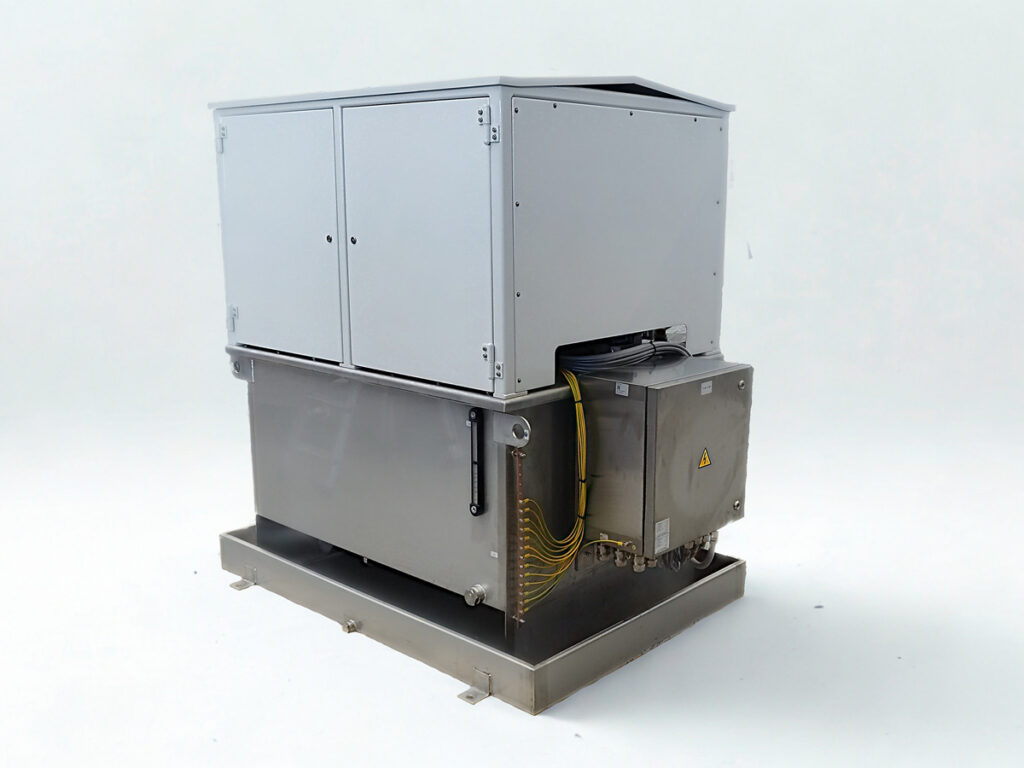
DESIGN AND COMPONENTS
Key Components Selected
– AISI-316 stainless steel tank, for maximum resistance in aggressive environments.
– C5M painted steel cover with inspection doors and panels.
– Variable displacement piston pump for dynamic performance.
– On/Off 24VDC solenoid valve.
– Proportional solenoid valve.
– Special custom-designed hydraulic cylinders with integrated transducer.
Selected Brands
– Atos: ATEX/IECEx pumps and valves.
– Siemens Innomotics: Special electric motors.
– MP Filtri: Oil filters.
– Trafag: Monitoring instrumentation.
System Performance
– Operating pressure: 180 bar.
– Flow rate: Variable.
– Circuit: Open.
Thermal Management and Filtration
– Pressure and return line filters.
– Breather filter on the tank, designed to operate up to +50 °C
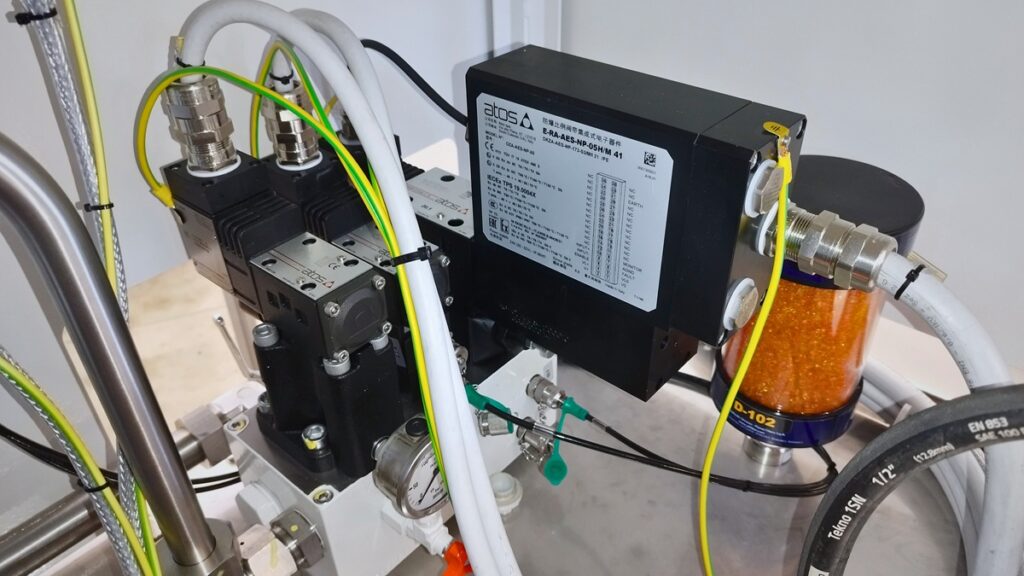
INNOVATION AND CUSTOMIZATION
Tailored Solutions
– Optimized layout according to client specifications.
– Design and manufacturing of custom hydraulic cylinders with integrated transducers.
– Customized nomenclature for clear management
Challenges Faced and Solutions
The selection of components required particular attention:
– Special Siemens/Innomotics electric motors, for compatibility with ATEX/IECEx regulations.
– ATOS solenoid valves, a leader in the production of components for classified environments.
– Coordination with TÜV to obtain full certification of the mechanical assembly, a novelty for this type of system.
Distinctive Features Compared to a Standard Power Unit
– Use of ATEX/IECEx certified electrical components.
– AISI-316 tank with integral cover.
– Certified electrical and electronic components.
– Armored cabling compliant with standards for explosive atmospheres.
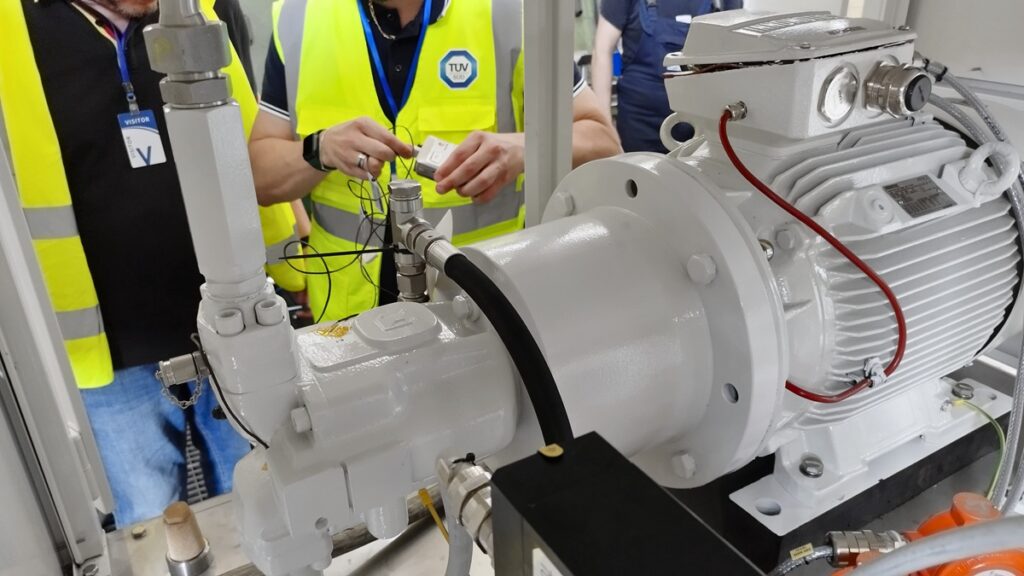
CONTROL, MAINTENANCE AND SAFETY
Sensors and Monitoring Devices
– 2 ATEX/IECEx level switches.
– 1 ATEX/IECEx thermostat.
– 2 ATEX/IECEx pressure switches.
– 1 AISI-316 JBox with ATEX/IECEx armored cables.
Diagnostics and Accessibility
– Although no digital predictive systems are implemented, the mounted sensors provide essential data for monitoring.
– Design focused on accessibility: simplified filter cartridge replacement and routine maintenance.
Regulatory Compliance
– The power units are classified as “partly completed machinery” according to Machinery Directive 2006/42/EC, with a declaration of incorporation (Annex II1B).
– Construction complies with UNI EN ISO 4413, which regulates hydraulic systems and components.
– ATEX/IECEx certification (voluntary internationally recognized standard for use in Hazardous Areas) on the entire mechanical assembly, validated by TÜV.
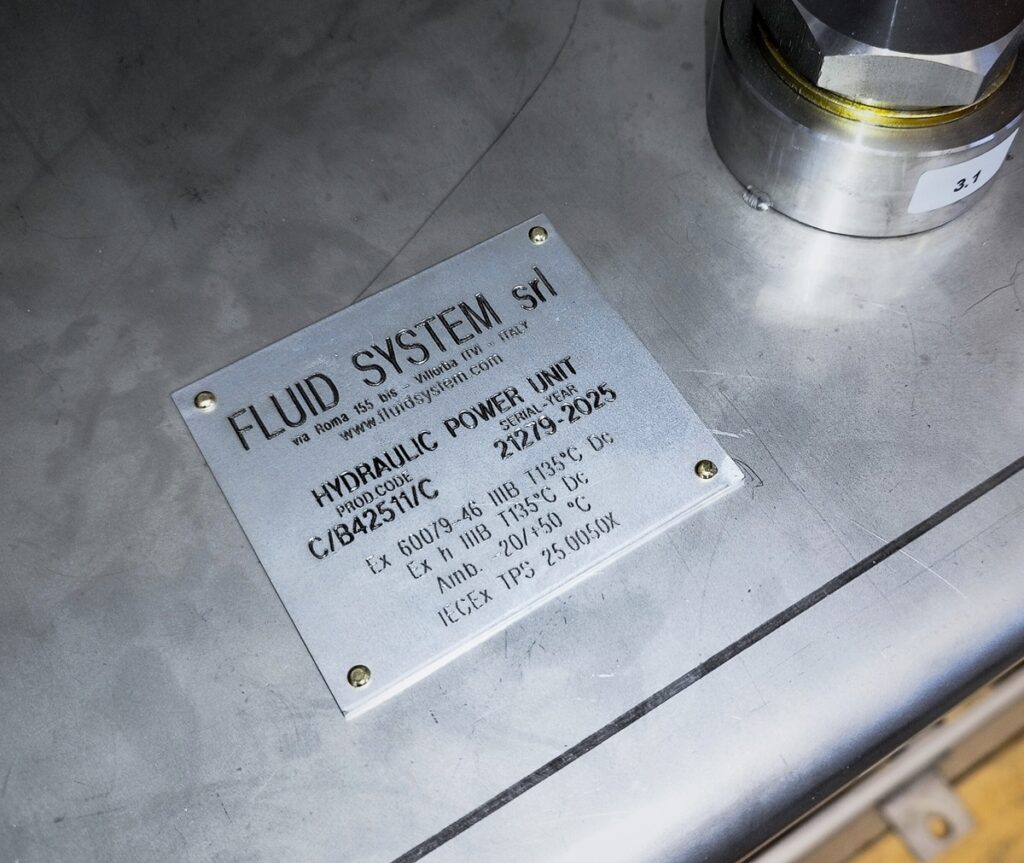
CONCLUSION
A project of high regulatory and technical complexity, managed entirely by Fluid System: from design choices to full system certification, including the selection of top-tier components and custom personalization. The two power units represent a new benchmark in the field of certified hydraulics for hazardous environments.
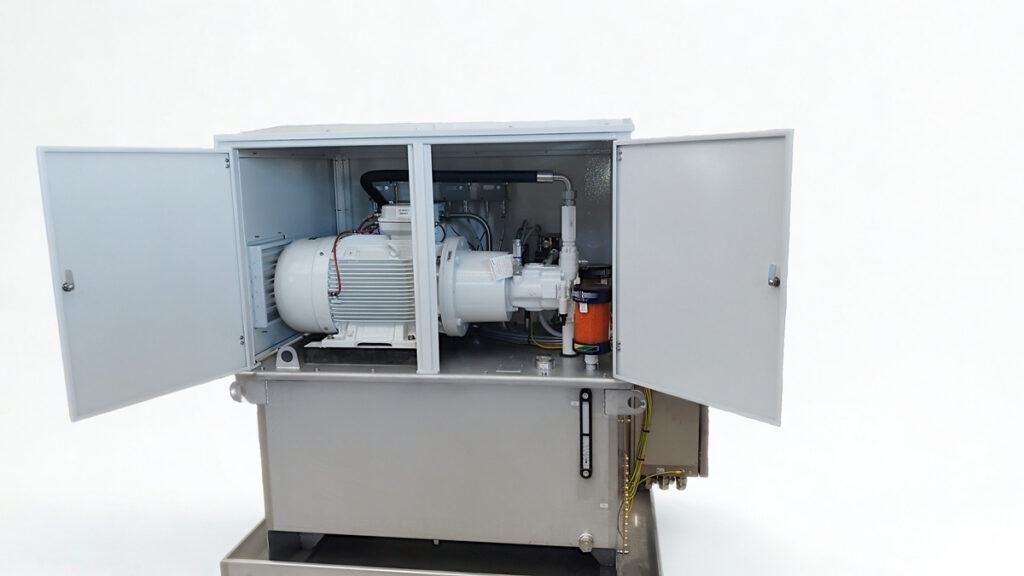